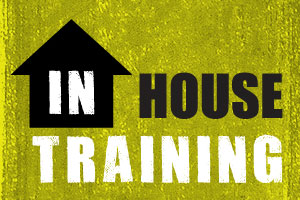
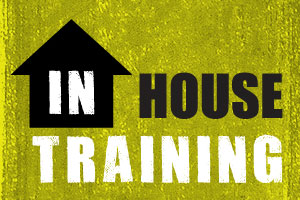
หลักการและเหตุผล
องค์การจะประสบความสำเร็จและเติบโตได้อย่างยั่งยืน จะต้องให้ความสำคัญกับเรื่อง “คุณภาพ” ในสินค้าและบริการ และให้ความสนใจต่อความสูญเสียจากความผิดพลาดในกระบวนการผลิต ทั้งกรณีความผิดพลาดจากวัตถุดิบ ความผิดพลาดจากชิ้นส่วนประกอบ ความผิดพลาดของเครื่องจักร ความผิดพลาดของชุดควบคุม ฯลฯ แต่สาเหตุของความผิดพลาดที่เป็นประเด็นสำคัญที่สุดสำหรับการควบคุมคุณภาพของกระบวนการคือ “ความผิดพลาดของพนักงาน” (Human Error)
แนวความคิดของการควบคุมคุณภาพของกระบวนการ (อ้างอิง AIAG) มีวัตถุประสงค์เพื่อ “การป้องกัน (Prevention) และการตรวจจับ (Detection)” ลักษณะข้อบกพร่องที่ก่อให้เกิดผลเสียต่อผลิตภัณฑ์ที่อยู่ในกระบวนการ (Process) และนำไปสู่การปฏิบัติการแก้ไขต่อไป ซึ่งจากแนวคิดดังกล่าว ถือว่าเป็นการพยายามควบคุมคุณภาพของกระบวนการ โดยดำเนินการขณะที่คุณภาพยังไม่ได้รับการสร้างให้เกิดขึ้นกับผลิตภัณฑ์ ซึ่งการควบคุมในระดับพนักงานต้องอาศัยกลไกมาช่วยในการควบคุม ตลอดจนการควบคุมในระดับจัดการต้องอาศัยสารสนเทศมาช่วยในการบริหาร
หนึ่งในกลไกการควบคุมคุณภาพระดับพนักงานที่สำคัญคือ การควบคุมด้วยระบบหยุดทันทีเมื่อมีความผิดพลาดเกิดขึ้น (Autonomation / Jidoka) ซึ่งแนวความคิดสำคัญประการหนึ่งของระบบดังกล่าวคือ ระบบการป้องก้นความผิดพลาด (Mistake Proofing / Poka Yoke) โดยการกำหนดกรอบในการเรียนรู้ที่สำคัญคือ ความผิดพลาดที่เกิดจากความเผอเรอของพนักงาน อันเป็นสาเหตุที่สำคัญที่สุดของข้อบกพร่องต่าง ๆ ในกระบวนการ ซึ่งการเรียนรู้จะให้ความสำคัญกับหัวข้อดังนี้
- ข้อบกพร่อง 10 ประการ ในกระบวนการผลิต (แนวทางของฮิราโน่)
- ความผิดพลาด 4 ประการ (Juran Research – งานวิจัยของจูราน)
- ความสัมพันธ์ของประเภทความผิดพลาดกับมาตรการตอบโต้ (แนวทางของจูราน)
- การค้นหาข้อบกพร่องและวิเคราะห์สาเหตุของความเผอเรอ
- กำหนดแนวทางการตรวจจับ (Detection) และการป้องกันความผิดพลาด
- กลไกป้องกันความผิดพลาด (หยุด / บังคับ / เตือน)
- ตัวอย่างของเทคนิคป้องกันความผิดพลาดต่าง ๆ
- เครื่องตรวจจับ (Detector) ที่นิยมใช้ในการป้องกันความผิดพลาด
วัตถุประสงค์ของหลักสูตร
- เพื่อให้ผู้เรียนเข้าใจความหมายคุณภาพ การประกันคุณภาพ หลักการควบคุมคุณภาพ และแนวคิดของการควบคุมคุณภาพของกระบวนการ ที่มีผลต่อคุณภาพของผลิตภัณฑ์ก่อนถึงมือผู้บริโภค
- เพื่อให้ผู้เรียนเข้าใจระบบการป้องกันความผิดพลาด (Mistake Proofing / Poka Yoke) มีแนวทางในการค้นหาข้อบกพร่องและวิเคราะห์สาเหตุของความเผอเรอ นำไปสู่การกำหนดแนวทางการตรวจจับ (Detection) และการป้องกันความผิดพลาด (Prevention) ในกระบวนการของตนเอง
รายละเอียดเนื้อหาตามหลักสูตร
Module - 1 พื้นฐานของการสร้างจิตสำนึกการป้องกันความผิดพลาดModule - 2 ความหมายและแนวคิดของคุณภาพในกระบวนการ
- กิจกรรมปรับคลื่นความถี่ของสมองก่อนการเรียนรู้
- แนวคิดในการทำกำไรของธุรกิจสมัยใหม่
- สร้างจิตสำนึกการปรับปรุงการทำงานด้วย “กรณีศึกษา”
- จิตสำนึกความเป็นเจ้าของกับการป้องกันความผิดพลาด (Ownership Quotient)
Module - 3 เครื่องมือและเทคนิคในการควบคุมคุณภาพของกระบวนการ
- ความหมายของคุณภาพและการประกันคุณภาพ
- แนวคิดของการควบคุมคุณภาพ (เชิงเทคนิคกับเชิงจัดการ)
- หลักการของการควบคุมคุณภาพ (Quality Control Principle)
- ตัวแบบ SIPOC กับการควบคุมคุณภาพของกระบวนการ
- ความหมายของการควบคุมคุณภาพของกระบวนการ (อ้างอิง AIAG)
- พีระมิดการควบคุมคุณภาพของกระบวนการ (Quality Control Pyramid)
- (1) ระบบการป้องกันความผิดพลาด POKA YOKE
ข้อบกพร่อง 10 ประการ ในกระบวนการผลิต (แนวทางของฮิราโน่)
สาเหตุของข้อบกพร่อง 10 ประการ
ตารางความสัมพันธ์ของข้อบกพร่องและสาเหตุ
ความผิดพลาด 4 ประการ (Juran Research – งานวิจัยของจูราน)
ความผิดพลาดจากความเผอเรอ
ความผิดพลาดจากเทคนิค
ความผิดพลาดจากความตั้งใจ
ความผิดพลาดจากการสื่อความ
ความสัมพันธ์ของประเภทความผิดพลาดกับมาตรการตอบโต้ (แนวทางของจูราน)
- แนวคิดสำคัญของระบบการป้องกันความผิดพลาด POKA YOKE
การค้นหาข้อบกพร่องและวิเคราะห์สาเหตุของความเผอเรอ
กำหนดแนวทางการตรวจจับ (Detection) และการป้องกันความผิดพลาด
กลไกป้องกันความผิดพลาด (หยุด/บังคับ/เตือน)
- ตัวอย่างของเทคนิคป้องกันความผิดพลาดต่าง ๆ
- เครื่องตรวจจับ (Detector) ที่นิยมใช้ในการป้องกันความผิดพลาด
- Activity I: ค้นหาข้อบกพร่องและกำหนดแนวทางการป้องกัน (วิเคราะห์กระบวนการ)
- Activity II: นำเสนอการวิเคราะห์ POKA YOKE แบบกลุ่ม
- (2) การควบคุมที่หน้างาน: แนวคิด 5ส และ Visual Control (Introduction)
- (3) การควบคุมด้วยสารสนเทศ: การควบคุมคุณภาพของกระบวนการโดยอาศัยสถิติ (Statistical Process Control – SPC) (Introduction)
เต็มใจให้คำปรึกษา : คุณบุษกร สุขโรดม (ผู้จัดการฝ่ายขาย)